The Wiped-Film / Short Path Distillation Process
Pope adds superior design and construction to the basic wiped-film/short path still process. This has enabled Pope stills to sustain pressures down to one micron for molecular distillation.
How Wiped-Film / Short Path Distillation Works
Wiped-film distillation is a highly efficient method for separating and purifying liquids in chemical processing, particularly useful for thermally sensitive materials with high boiling points. The process is also known as Molecular Short Path Distillation, Thin Film Distillation, and Short Path Evaporation.
Here’s an in-depth look at how Pope’s Wiped-Film Distillation equipment operates:
- Feed Introduction: The process begins with the continuous feeding of the liquid onto the inner wall of a heated vertical cylinder. This ensures a steady and controlled introduction of the material to be distilled.
- Film Formation: Rotating wipers spread the liquid into a thin film across the heated cylinder’s surface. This film formation is crucial as it maximizes the surface area for heat transfer, ensuring efficient and uniform heating of the liquid.
- Evaporation: The thin liquid film allows for rapid and efficient heat transfer, causing the more volatile components to evaporate quickly. This rapid evaporation is key to preventing thermal degradation of sensitive materials.
- Condensation: The vaporized components travel a short distance to a nearby cool surface (condenser), where they condense into a liquid distillate. The close proximity of the condenser to the evaporation surface is a critical design feature that enhances the efficiency of the condensation process.
- Residue Collection: Heavier, less volatile components remain in liquid form and are collected as residue. The design ensures that these components do not have extended exposure to high temperatures, which could cause degradation.
- Temperature and Vacuum Control: The system is designed to handle high temperatures up to 300°C and vacuum levels as low as 0.001 torr. This capability allows for the distillation of high boiling point materials at lower temperatures, reducing the risk of thermal decomposition.
- Operational Parameters: Key parameters that can be adjusted include the feed rate, still body temperature, and vacuum level. These adjustments help optimize the distillation process for maximum efficiency and product purity. Skilled operators can fine-tune these settings to enhance throughput and yield.
- Efficiency Features: The wiping action ensures the liquid film remains even and homogeneous, preventing issues like dry spots and ensuring consistent processing. The design of the wipers, with diagonal slots, promotes turbulence and micro-mixing, further enhancing mass and heat transfer.
Pope’s wiped-film distillation equipment is versatile and reliable, making it suitable for a wide range of applications from lab-scale experiments to full-scale production. Its design ensures high-purity separation with minimal thermal degradation, making it a preferred choice for processing sensitive materials.
- Wiped-Film Distillation Process
- Wiper Diagram
Typical Applications of Wiped-Film Molecular Stills & Evaporators
- Biomaterial Concentration
- Molecular Distillations of Esters, Fatty Acids, Mono, Di, Omega 3 & Triglycerides
- Vitamin, Nutraceutical, Essential Oil Isolation
- Oil Deodorization
- Water Removal – ppm Level
- Solvent Recovery
- Vacuum Distillation of Terpenes, Terpenoids
- Chlorophyll, Phytosterols, Fat & Wax Removal, with clear distillate
- Purification After Extraction, (supercritical CO2, butane, hydrocarbon, ethanol, etc.)
- Concentration of Botanicals & Essential Oils
- Fractional Distilling via Hybrid Technology
- Improved Evaporation over Rotary Evaporators, Kugelrohr & Rotovap Apparatus
Definition of Molecular Distillation:
- Distillation that is carried out under a high vacuum in an apparatus so designed as to permit molecules escaping from the warm liquid to reach the cooled surface of the condenser before colliding with other molecules and consequently returning to the liquid and that is used in the purification of substances of low volatility.
- Vacuum distillation in which the molecules of the distillate reach the condenser before colliding with one another.
- Distillation in which a substance is heated under vacuum, the pressure being so low that no intermolecular collisions can occur before condensation.
Turnkey Processing Equipment
Pope offers turnkey processing equipment custom-built for your unique application.
Find Your Application
Learn how our tailored solutions can help you drive innovation and efficiency in your industry.
Request A Quote
Pope can help you identify the right solution for your processing needs.
Wiped-Film Gallery
View our gallery of Wiped-film systems including standard systems and customized solutions.
Complete Molecular Still Package System with electric band heating (bands removed), external condenser, all utilities, plus optional feed pump.
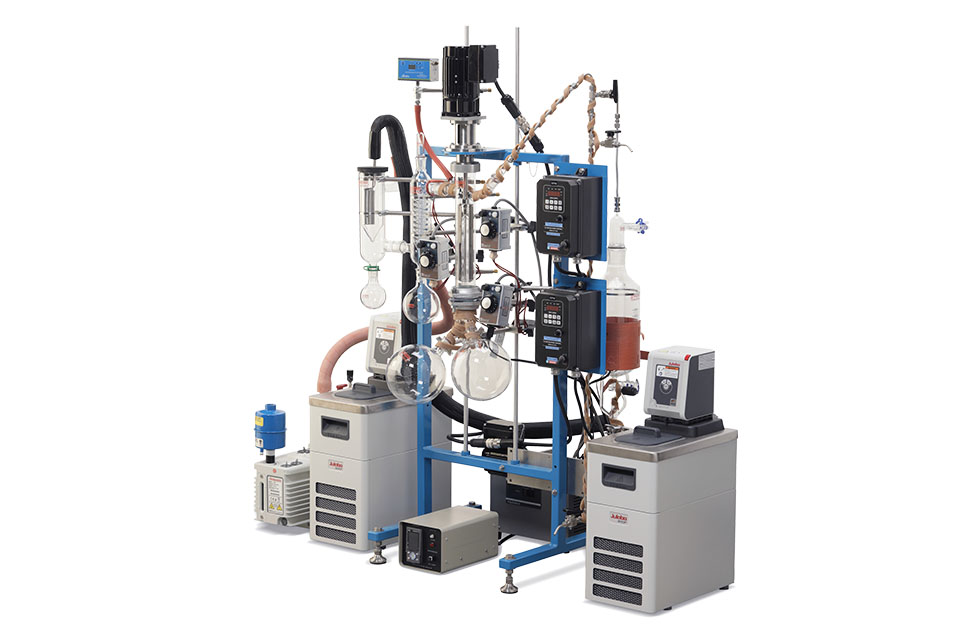
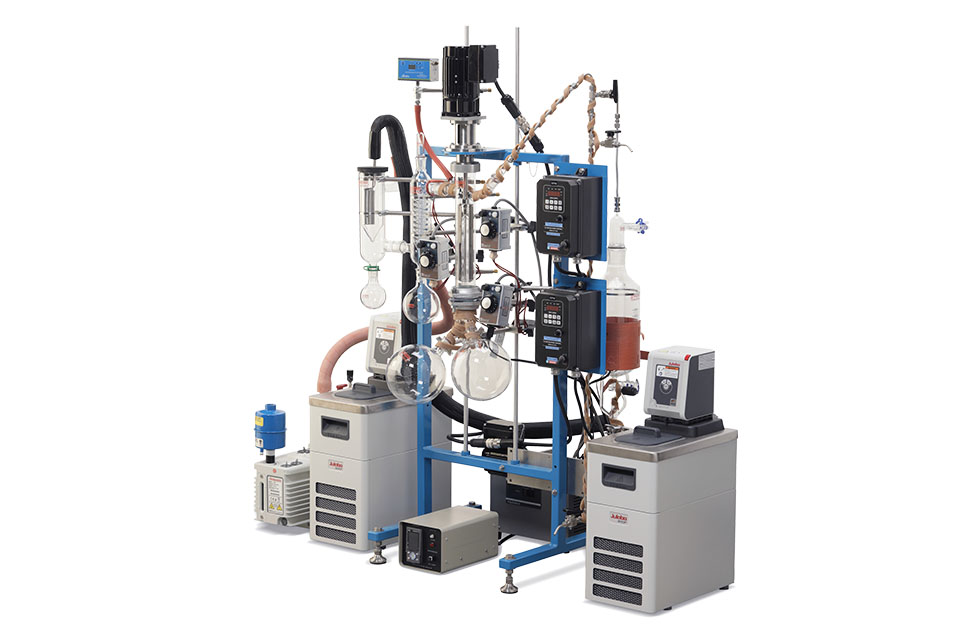
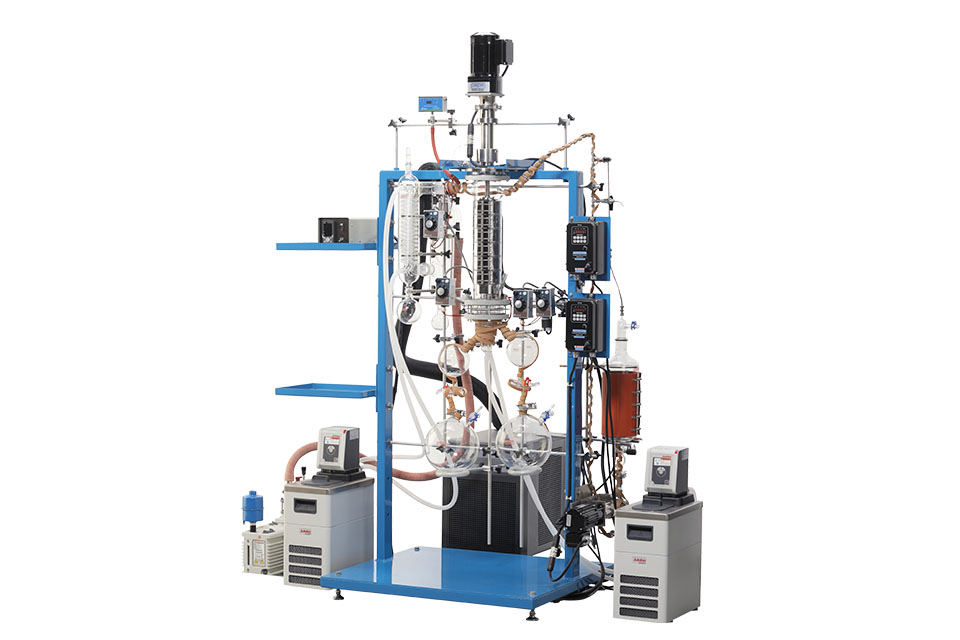
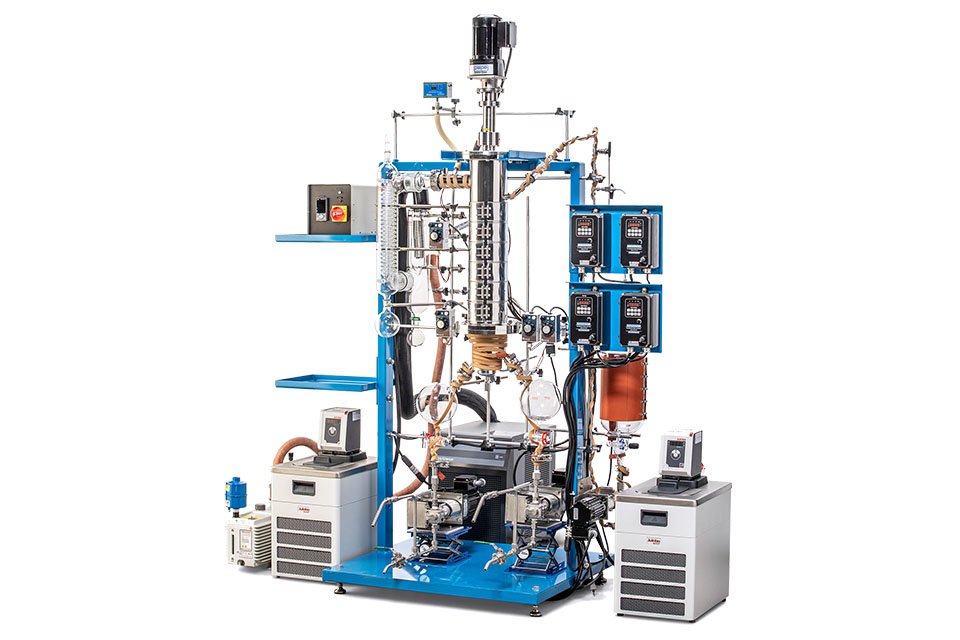

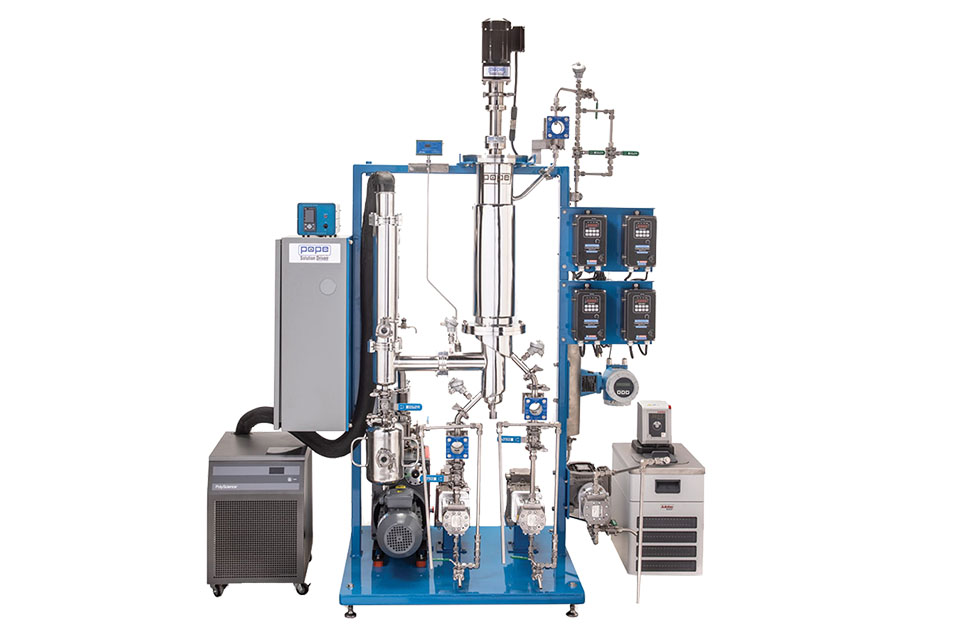


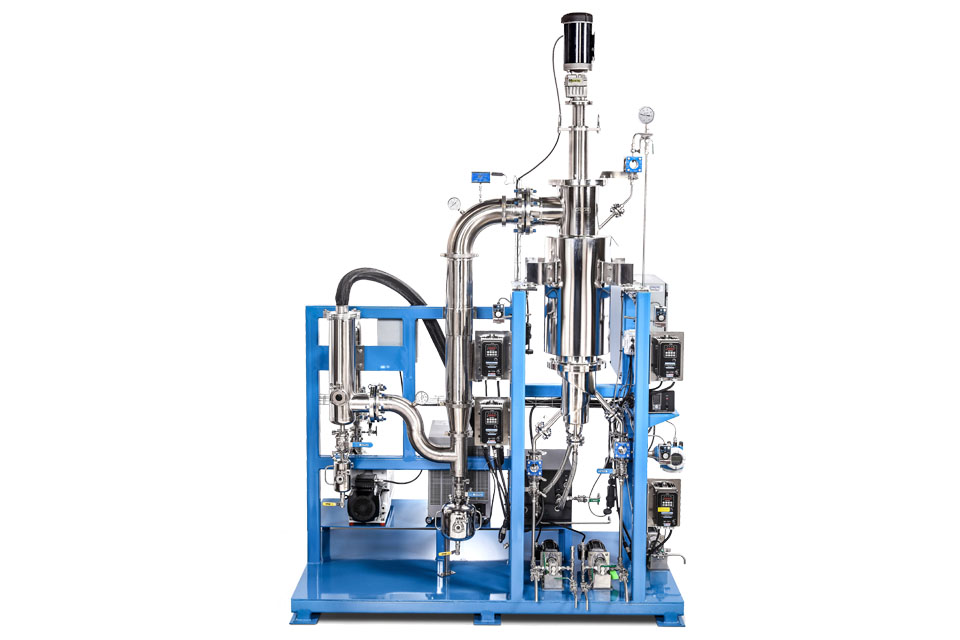
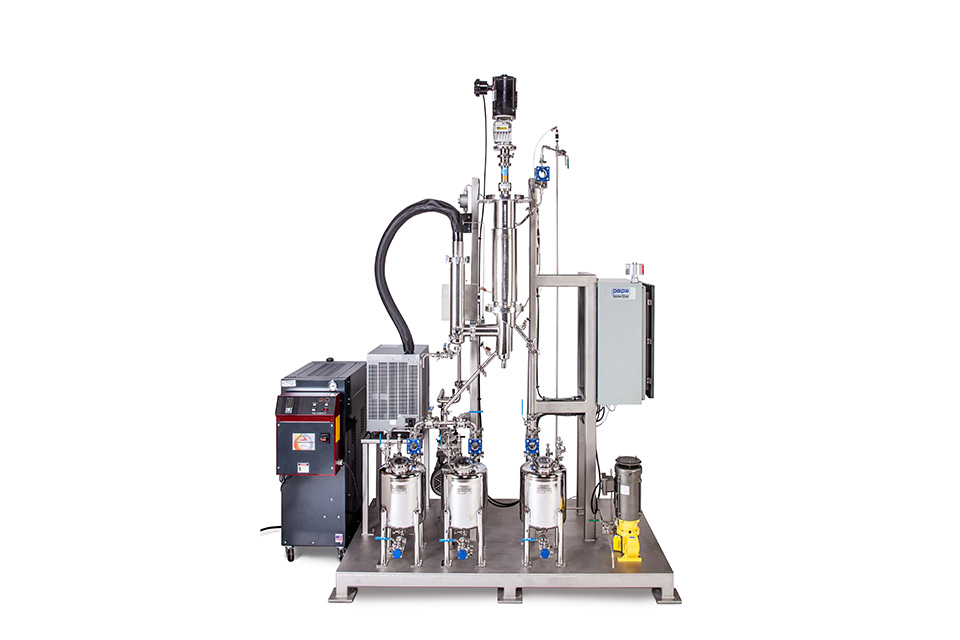
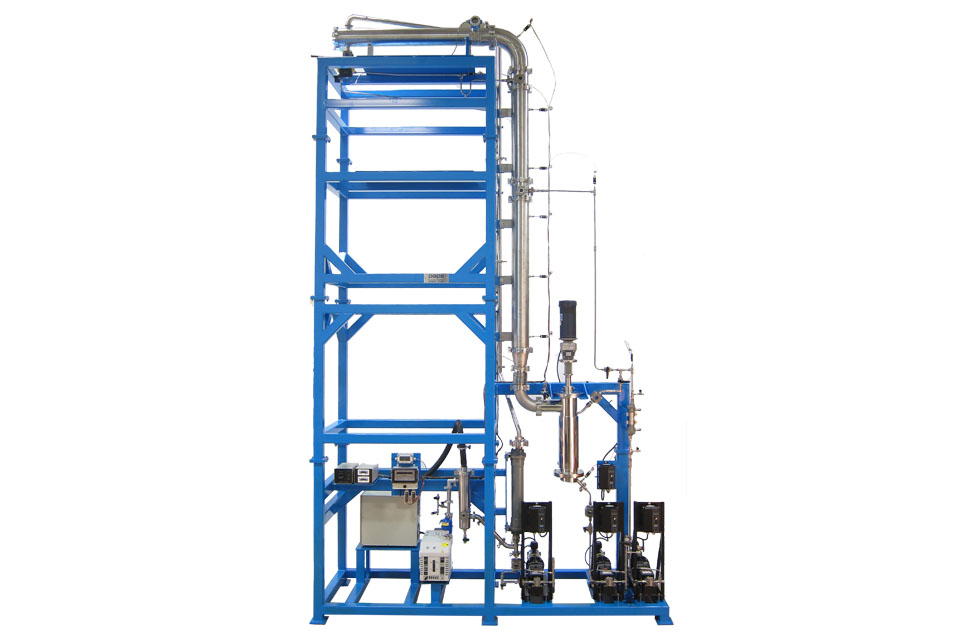
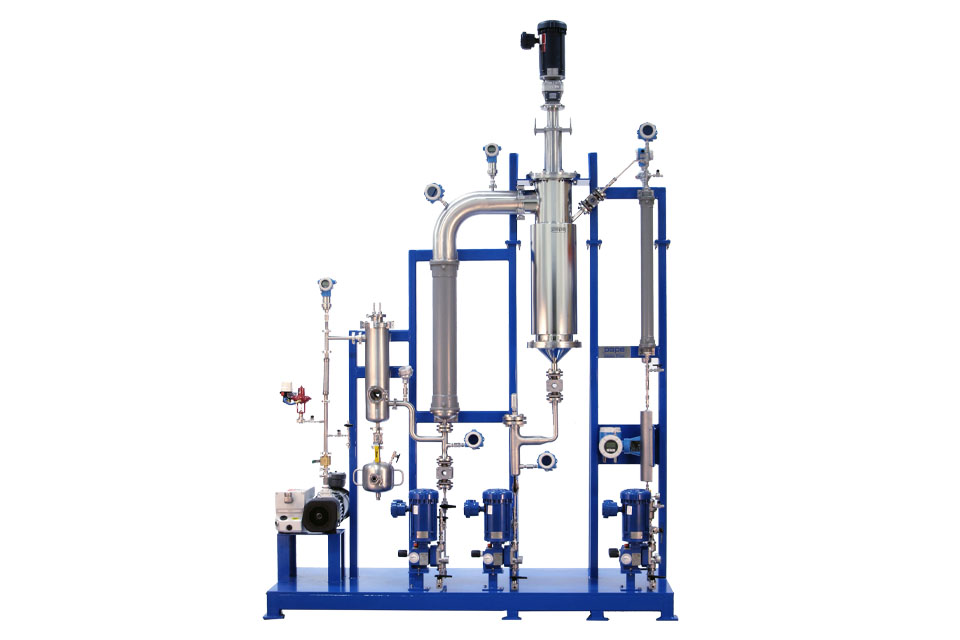
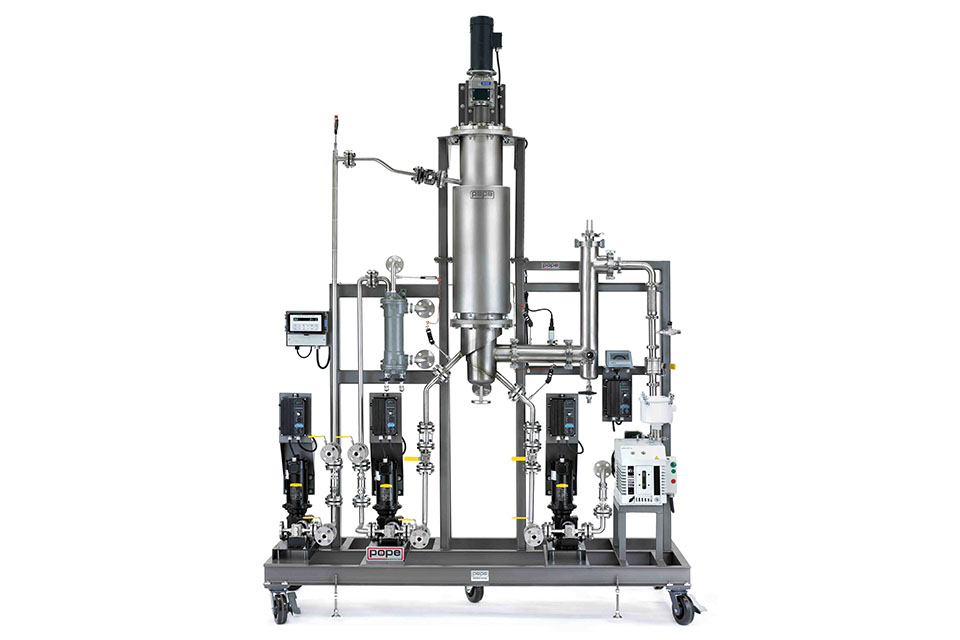
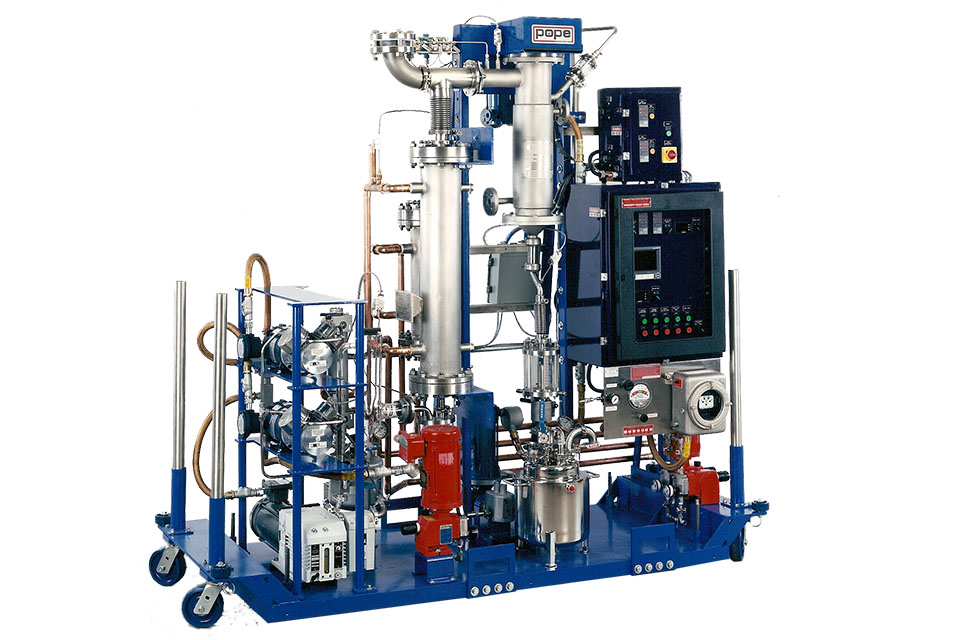


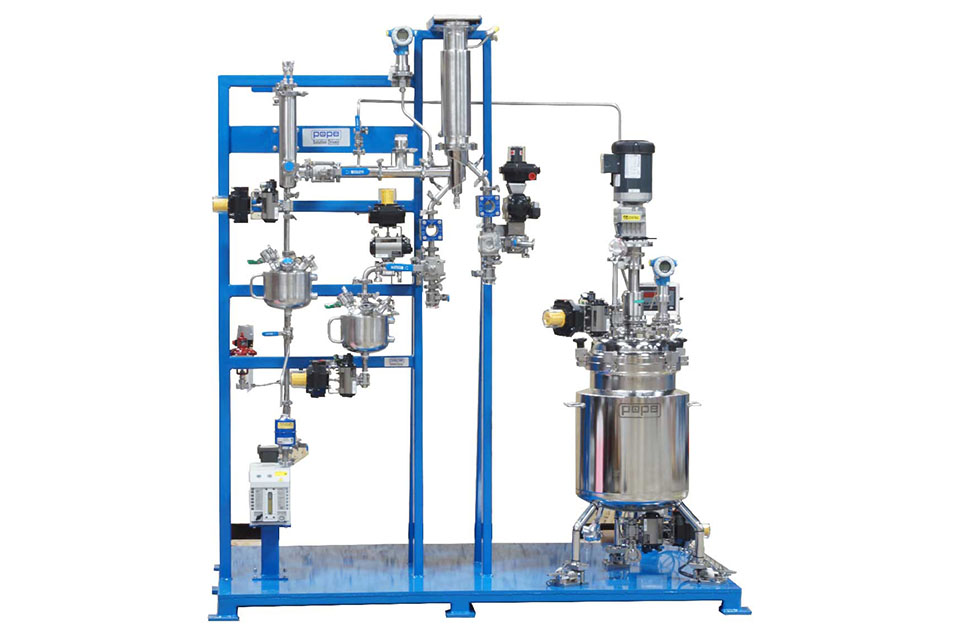
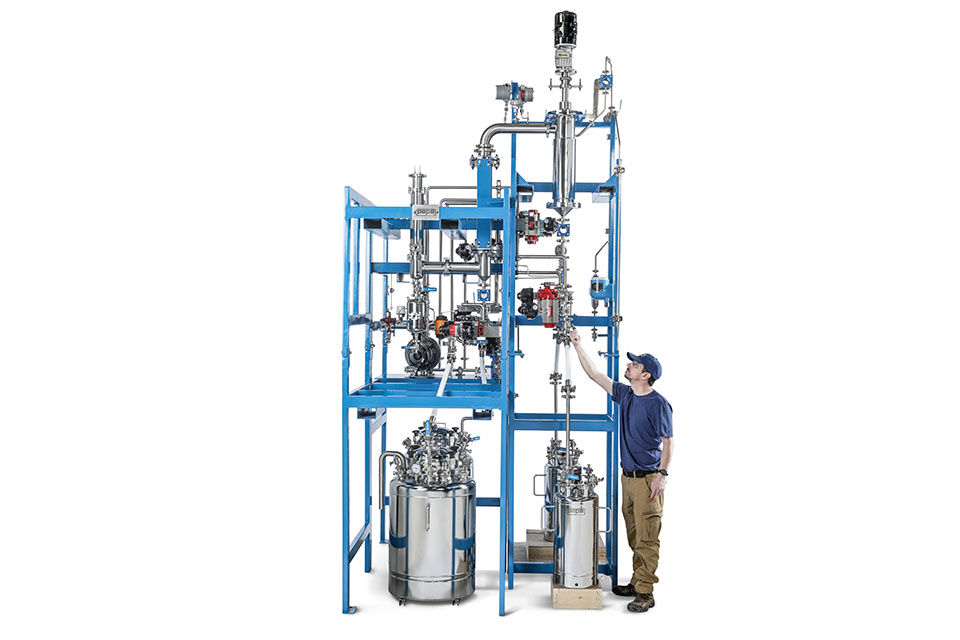
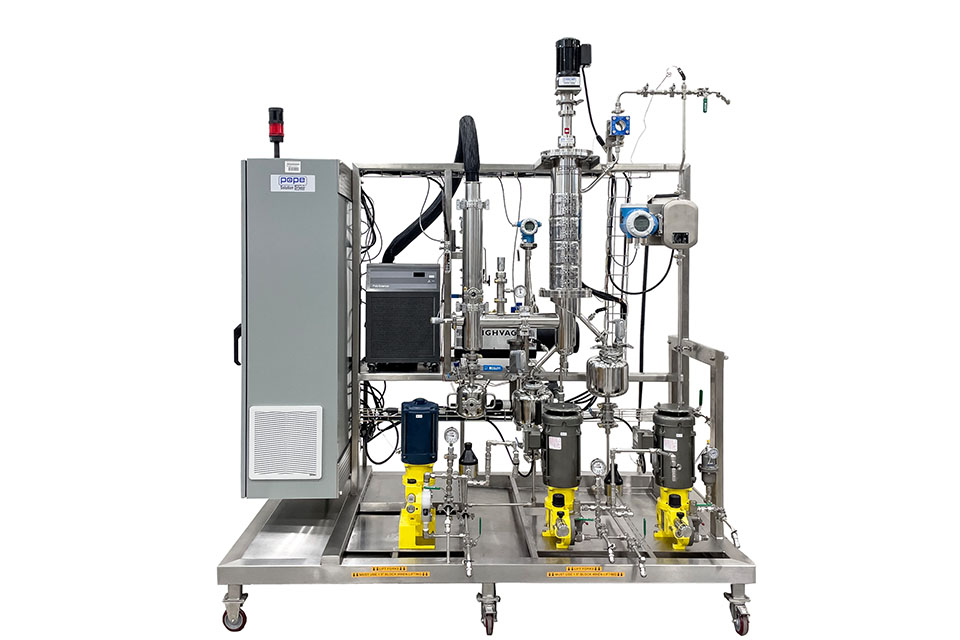
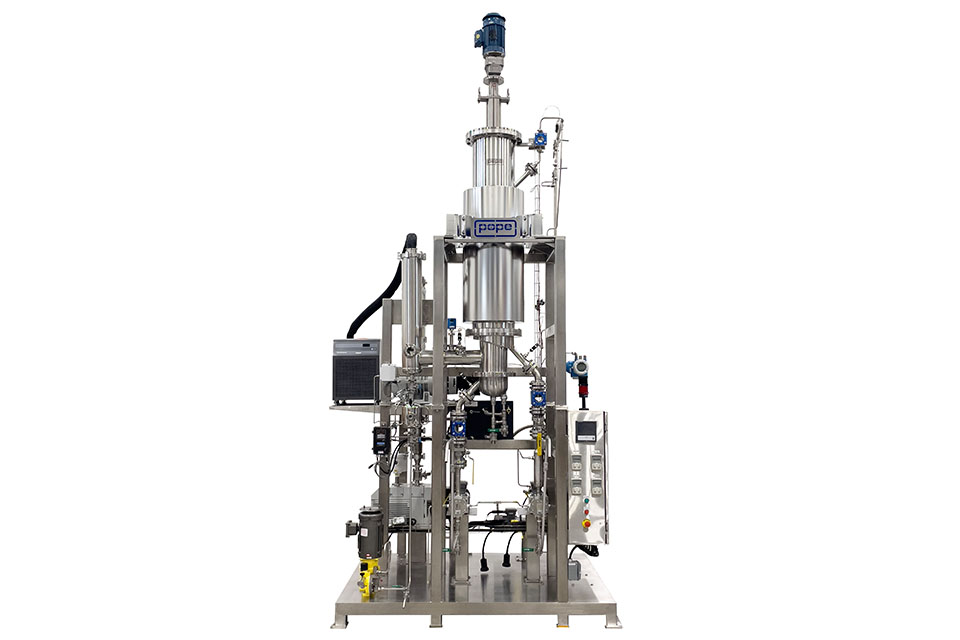

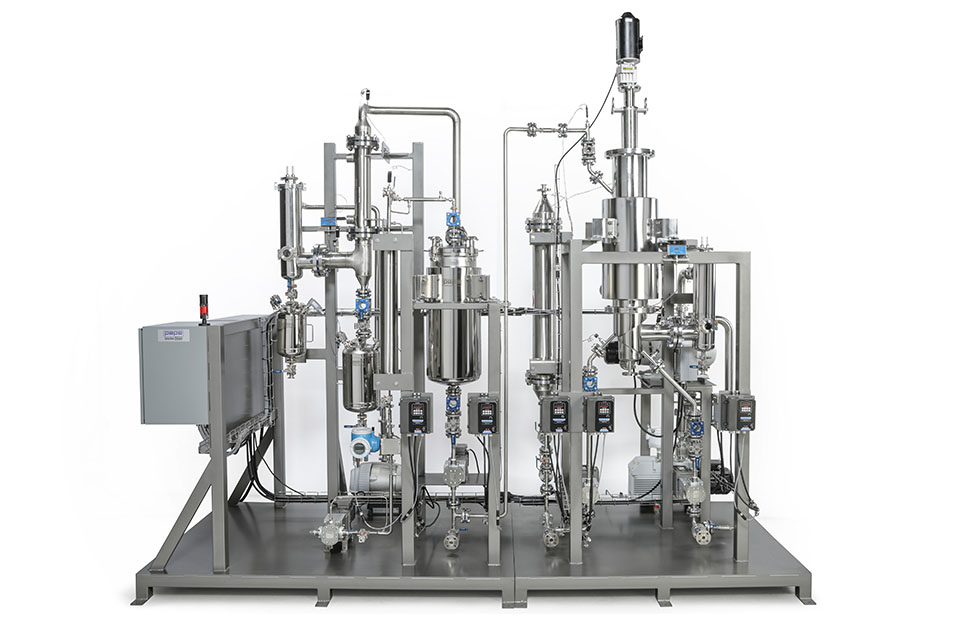

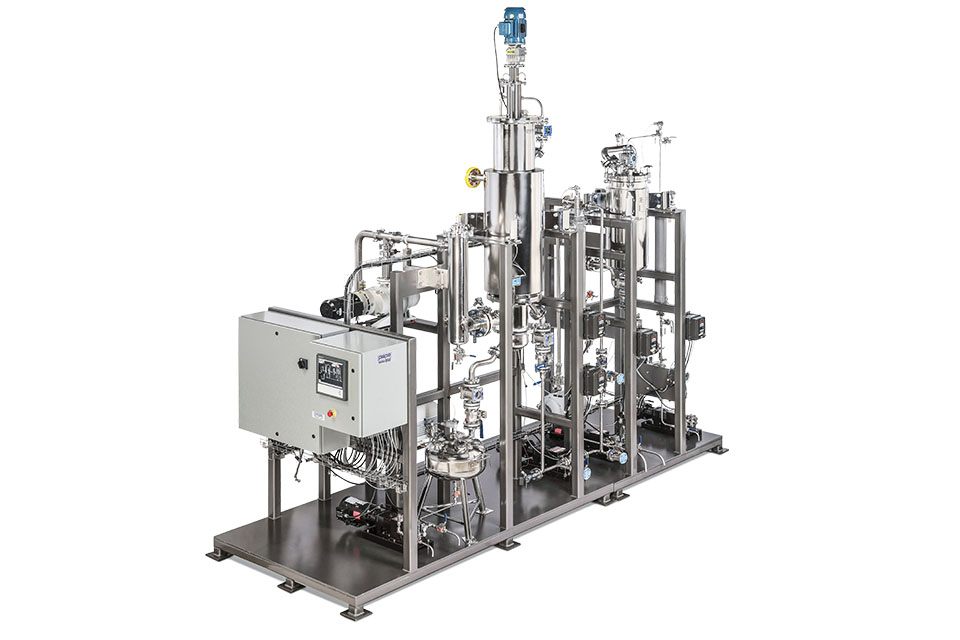
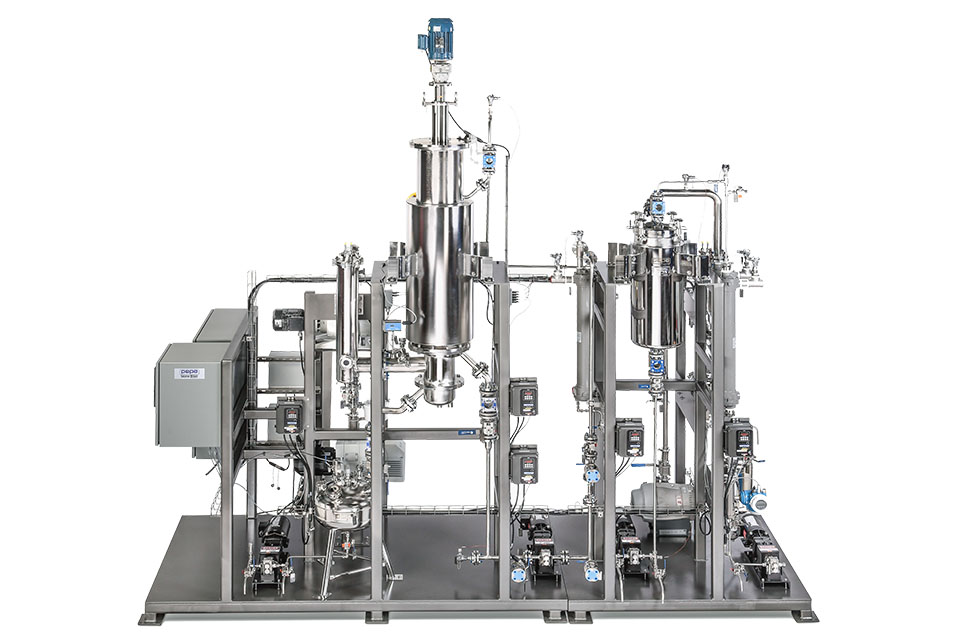
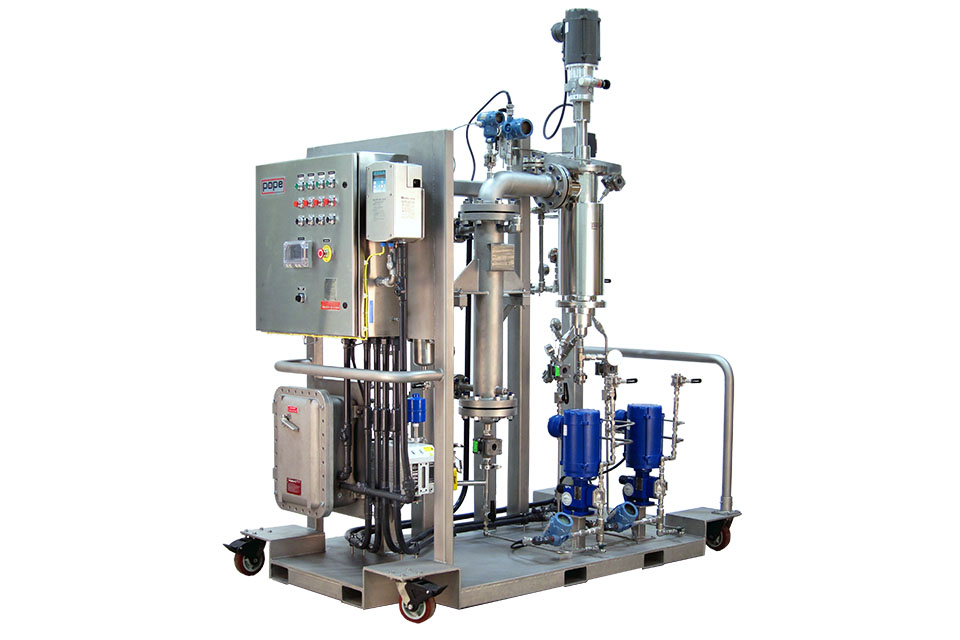

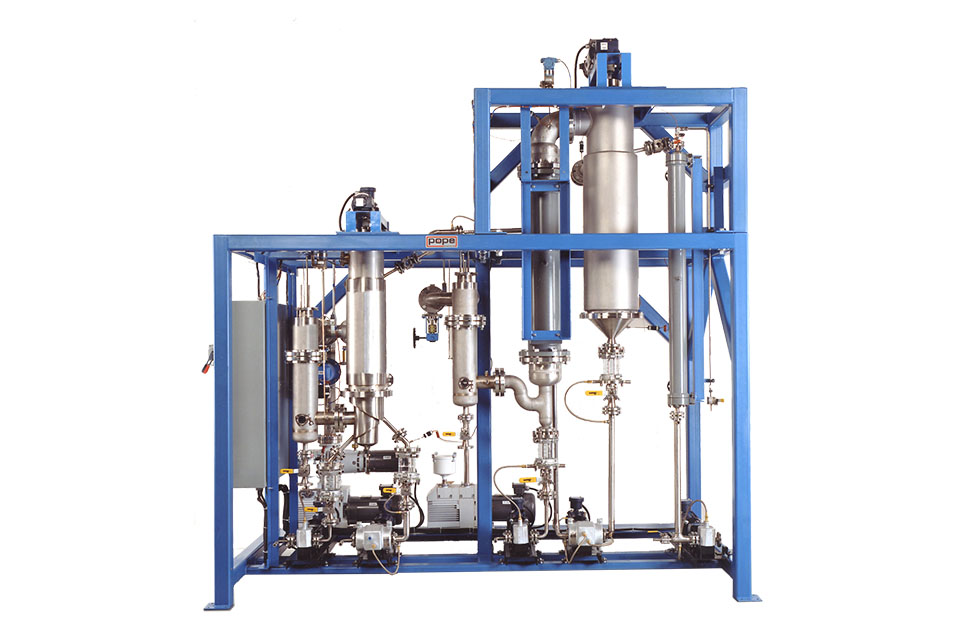
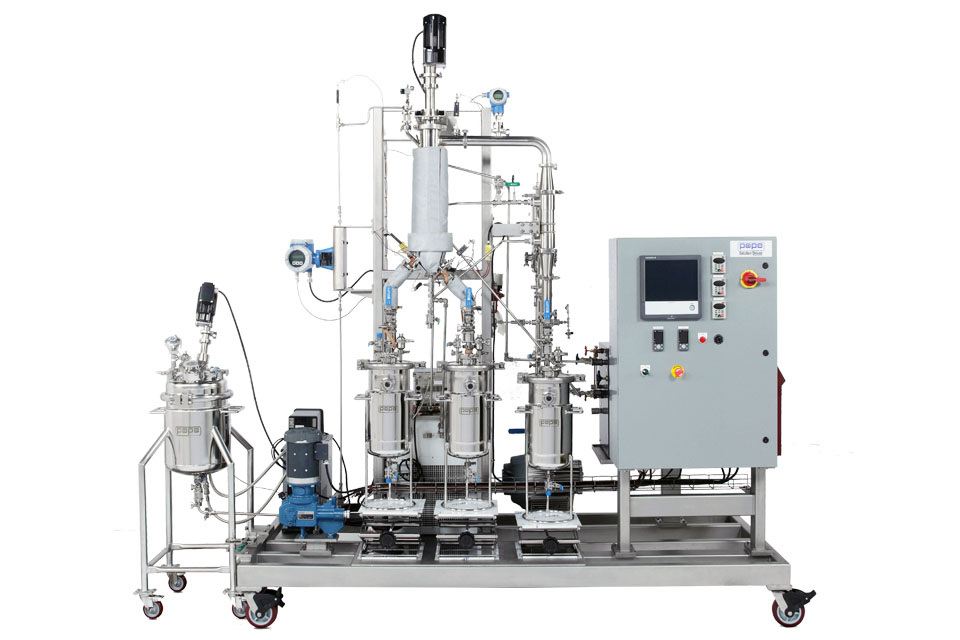
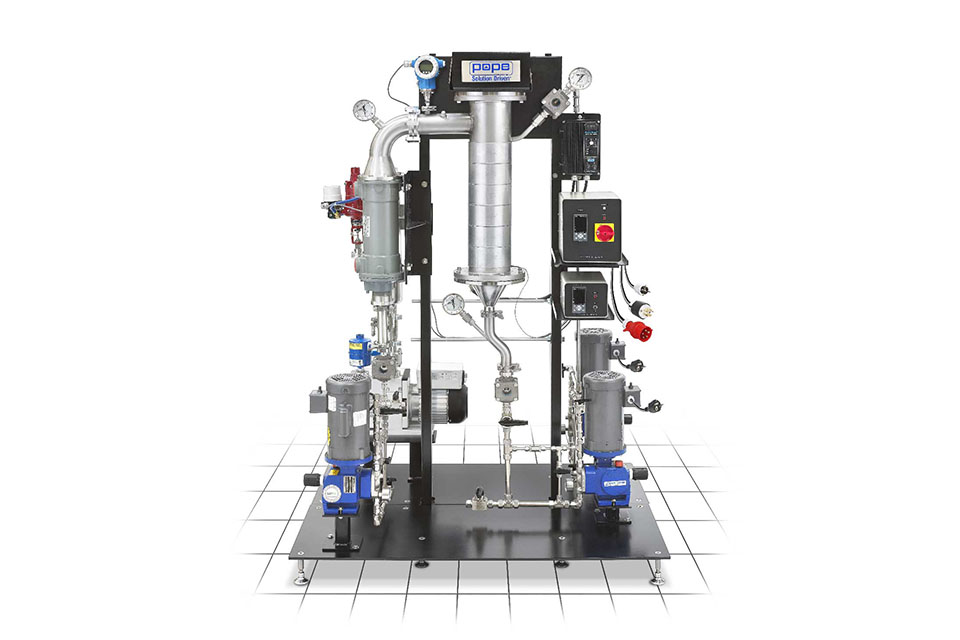
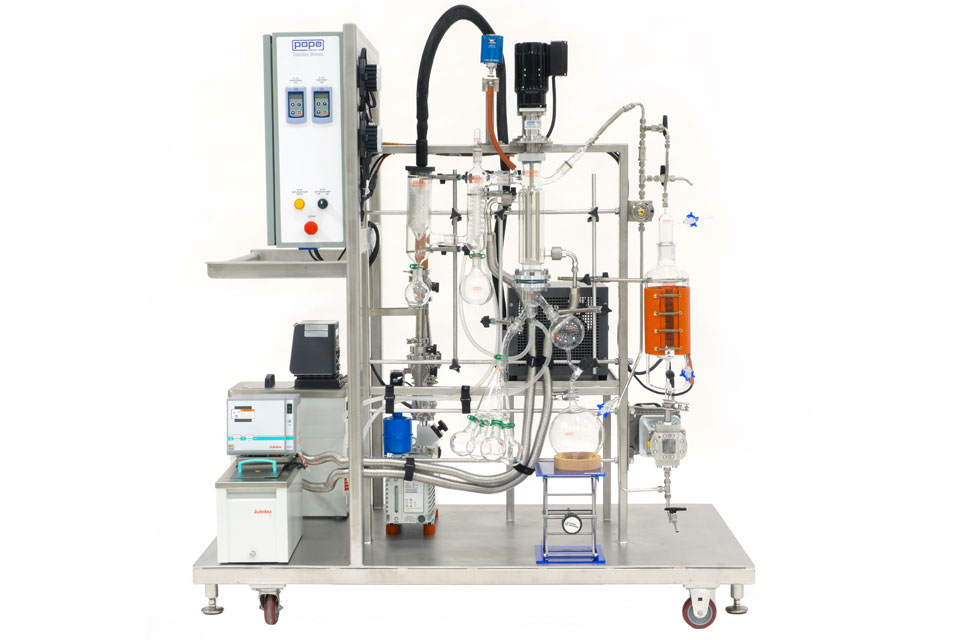
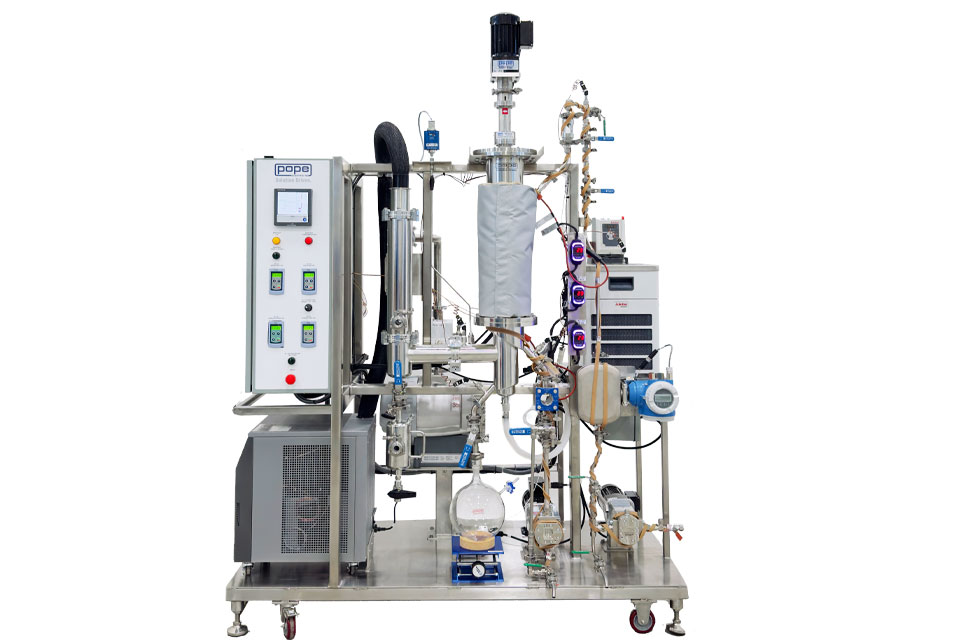