Polymer Devolatilization & Purification Equipment
Transform your polymer processing and create superior and new products with Pope’s polymer distillation equipment and technology. Remove both light and heavy contaminants, resulting in the highest quality, purity, and yield. Pope sets the standard, addressing the core challenges in the industry. In addition, Pope offers in-house feasibility testing, process development, and Toll Processing to assist in the development and manufacture of new products.
Our Equipment Our ServicesWhat is the process of Polymer Devolatilization?
For optimal purification of polymers, specialized wiped-film molecular distillation equipment plays an important role as a final or near-final process step. In the manufacturing of polymers, reactions are run where monomer building blocks in a solvent base are joined together to create polymer chains of desired lengths. In many of these reactions, an excess of monomer is maintained to keep the polymerization process going in a controlled, predictable manner. After these reactions, the polymer product will contain shorter chains, monomers, solvent and other lower boiling point contaminants which must all be removed. In some applications such as biopolymer implants and injections into patients, it is absolutely critical that not only solvents be removed but monomers and short chains as well. Silicone breast and other types of implants where these were not removed led to the major medical problems of years past.
Because these more volatile components have significantly lower boiling points than the main product, distillation is the preferred means of removal. But simply boiling of the polymer products in batch vessels, even under vacuum, for evaporating off of the lighter components can cause more problems than it solves. The heat exposure time which can go on for hours or longer, often causes degradation including breaking of the chains into shorter chains and monomers as well as causing cyclization of chains, forming a well known biologically hazardous contaminant. Where the polymer is high in viscosity, batch devolatilization will take considerably longer due to mass transfer limitations, making the problem worse.
Wiped-film distillation processing of these products is a significant improvement in polymer devolatilization. The polymer distillation equipment is designed to reduce heating exposure time from hours to seconds under high vacuum in a continuous flow through a heated wall with rotating wipers, creating a very efficient evaporation. The pressure drop under high vacuum conditions in the system is greatly reduced via the condenser surface being a very short distance (short-path) from the evaporation surface, aiding in the overall efficiency or the process resulting directly to increased purity and yield of final product. There is normally a prior pass through another wiped-film still to remove dissolved gasses and light solvents, enabling the second pass, removal of monomers and short chains, to perform optimally, at greater vacuum levels without undesired flashing.
Key Features of Our Polymer Devolatilization Equipment:
- Designed for the gentlest silicone purification distillation possible for polymer material applications via high vacuum and short residence time design.
- Precision Engineering:Our Wiped Film equipment is meticulously designed for optimal performance, ensuring precise devolatilization and separation & removal of different size monomers, oligomers, etc.
- Efficient Residue Removal: After removal of light fractions and undesired monomers and oligomers, longer chain product fractions may subsequently be distilled away from heavier contaminant residues, separating the target product as a “heart cut”.
- Adaptable to Diverse Industries:The same equipment designed for plastics, polymers, rubber, etc., can also be adapted for additional applications, including waxes, oils, specialty chemicals, etc. Our solutions cater to a spectrum of industries, providing versatile applications.
- Scalability: Pope’s Wiped film Stills utilize the same mechanism from lab to pilot plant, to production processing scale. What is done in the lab will pertain to the the larger scales, etc., and sizing of equipment is readily possible.
Process Applications:
- Devolatilization and Degassing of Prepolymers, Biopolymers
- Purification of Epoxy Resins, Latexes, Isocyanates, Urethanes, Silicones, Acrylics and others
- Removal of cyclic siloxanes from silicones including Polysiloxane Oils
- Purification & Concentration of Monomers
- Purification & Concentration of Polymers, Plasticizers, UV Inhibitors
- Stripping Monomers from Polymers
- Separation between Monomers, Dimers, Trimers, etc.
- Purification of Adhesives
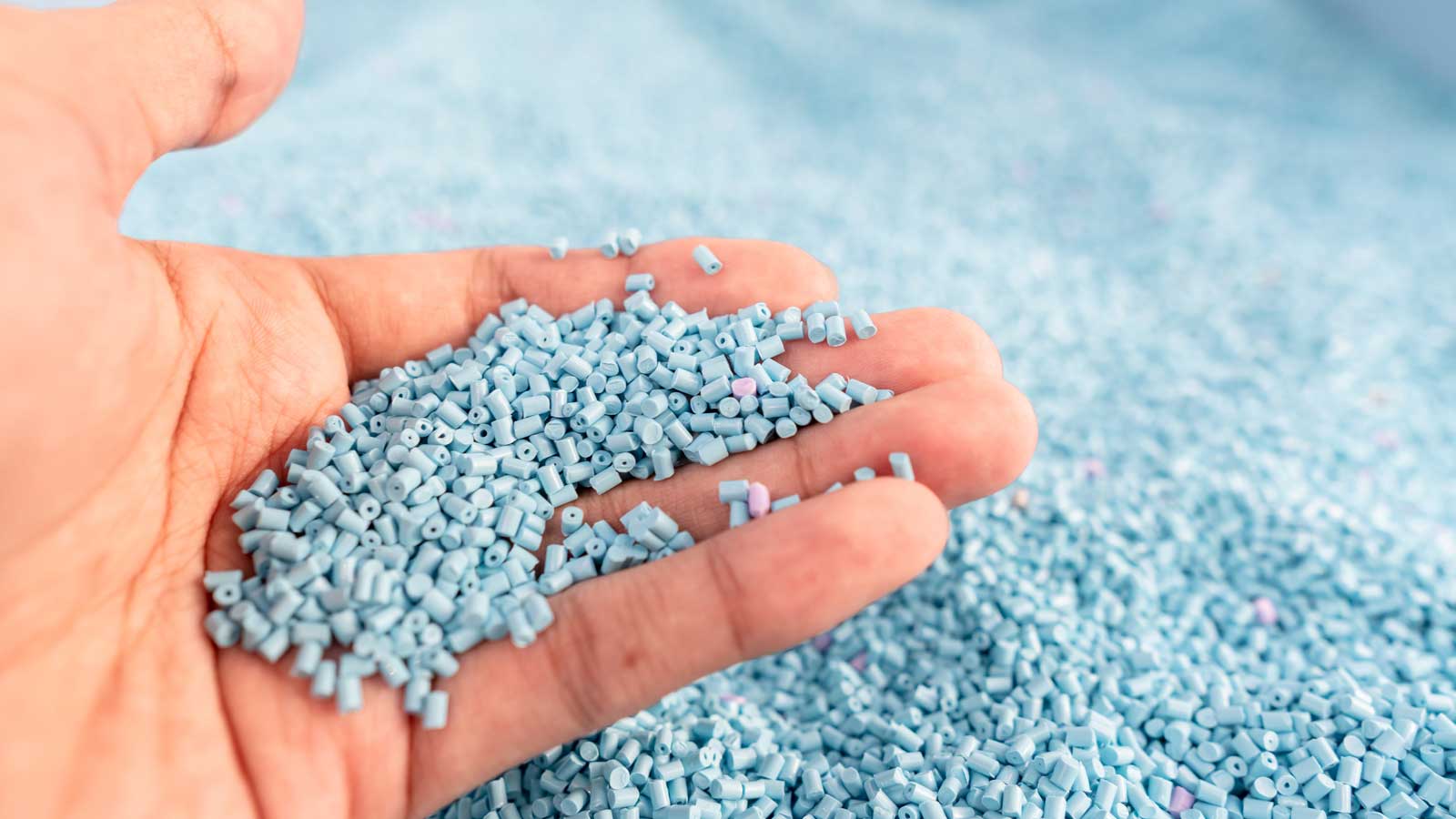
Our Equipment & Services
Transform your polymer processing with our polymer devolatilization equipment.
Request A Quote
Pope's equipment and services can help you meet the requirements of your industry. Contact us for more information on how we can tailor equipment for your applications.